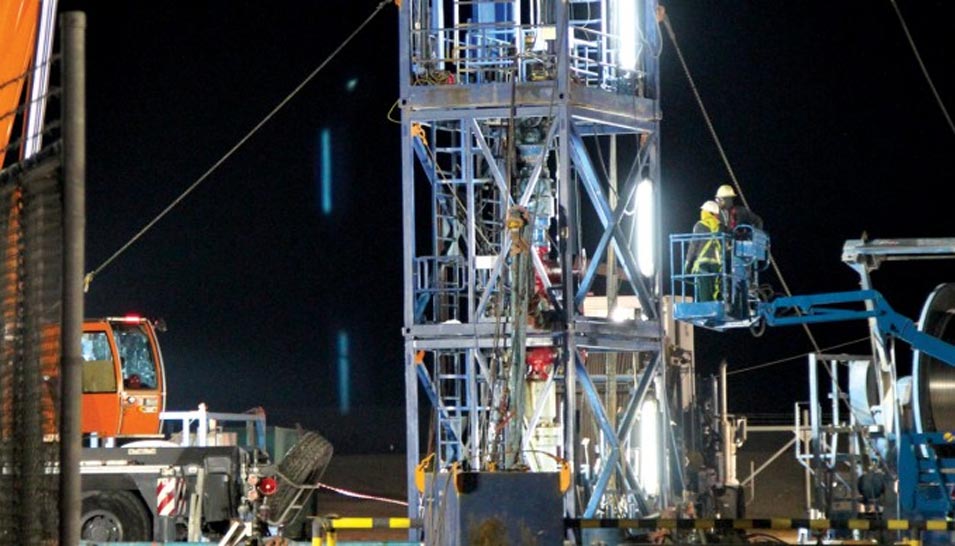
The TransCoil rigless deployed electrical submersible pumping system is first designed to bring wells on production faster with lower installation and replacement costs. The new system eliminates the need for an expensive rig to replace ESPs and is particularly useful in offshore wells where rig intervention is expensive and sometimes unavailable.
Saudi Aramco has announced the successful installation and functional test of the collaboratively developed Baker Hughes TransCoil rigless deployed electrical submersible pumping (ESP) system.
Designed to bring wells on production faster with lower installation and replacement costs for ESPs. By eliminating the need for an expensive rig to replace the ESP, it is particularly advantageous in offshore wells where not only rig intervention costs are expensive, but also where limited rig availability can delay ESP replacement.
“With our large ESP installation base, including many ESPs installed in our offshore fields, the ability to rapidly deploy ESPs riglessly provides tremendous cost reduction to our overall operations. The TransCoil system is particularly beneficial in our challenging high H2S fields as the premium metallurgy TransCoil can significantly extend the ESP operational life in harsh environment wells,” says Nasir K. Al Naimi, vice president of Petroleum Engineering and Development. “Collaboratively working with Baker Hughes, we have developed a solution that meets our immediate challenges and enables our long-term vision of one day ESP change-out.”
Home to more than 1,500 ESP installations with more than 100 change outs per year in a harsh production environment, Saudi Aramco is constantly developing ESP technologies to reduce change-out time and improve run life.
Because ESPs require a time-consuming rig installation on jointed tubing, the need for a more rapid rigless solution is critical for future operations.
How it Works
Conventional ESPs need workover rigs for deployment and their power cables are connected from the ESP bottom. In contrast, the TransCoil system is rapidly deployed with a coiled tubing (CT) unit into already installed production tubing, reducing deployment time from days to hours.
The technology also features an inverted ESP system with the motor connected directly to the powered CT. By eliminating the traditional ESP power cable-to-motor connection, the technology further improves overall system reliability.
The combination of the power cable and the CT into a cohesive deployment string extends the operating range of the TransCoil system to 12,000 feet and enhances reliability, compared to existing CT deployed ESPs that simply pull the power cable through the CT. The TransCoil nickel alloy outer jacket also provides corrosion protection in harsh environments.
Field Testing
The Khurais field was chosen to be the initial field trial location for the TransCoil system, with months of pre-job planning ensuring the trial’s success. The unique nature and complexity of the operations required multiple reviews both within Saudi Aramco and with the outside service providers. Weekly meetings addressed the job challenges of this new technology and helped develop the teamwork necessary for the successful field trial outcome.
Rigless operations to install the ESP commenced in mid-December 2016. Deployment operations of the TransCoil system went smoothly and the first-time rigless operations proved efficient in reducing installation time nearly 50% over the rig-based installation.