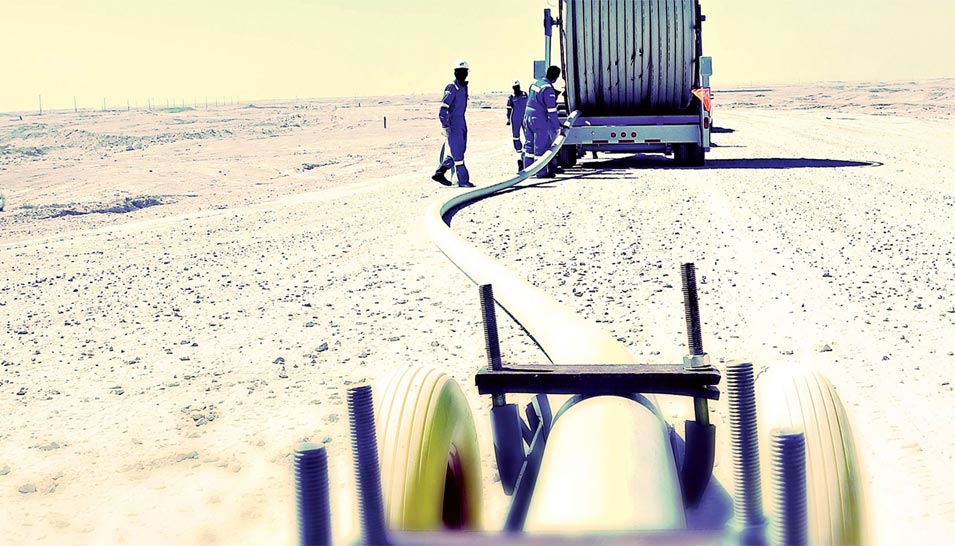
Crews work to lay down Reinforced Thermoplastic Pipe (RTP) on a Saudi Aramco project. With the advent of RTP on major oil and gas projects, companies such as Saudi Aramco have been able to achieve significant savings not only in direct cost, but also project length throughout the project life cycle.
The worldwide adoption of Reinforced Thermoplastic Pipe (RTP) in construction projects dates back to the early years of the 21st century as the technology drove cost saving initiatives by providing sustainable corrosion control measures.
However, the early uses of RTP technology were constrained by the application limitations of the manufactured pipes, which was reflected in maximum sizes, fluid pressures, and temperatures of the process designs. These application limitations have been progressively eased by advances in materials and manufacturing technology, requiring companies to stay abreast of developments in the field.
At Saudi Aramco, this is not necessarily a straightforward process. In larger companies, interdependent departments play various roles to validate, approve, and collaborate with vendors in an effort to reassure the safety and reliability of adopted technologies. In this context, Project Management and Engineering Services have had success in progressively deploying RTP in Onshore Maintain Potential Projects Department (OMPPD) oil and water service projects, working with vendors and other departments to introduce proven technological advancements that have produced significant savings for Saudi Aramco.
Early Adoption
OMPPD first deployed RTP back in 2015 in the Khurais and Central Arabia areas. The project scope included a 142-kilometer (km) length of 4-inch fiber reinforced RTP pipe with two suppliers where the oil applications required low design conditions (i.e., 1,500 pounds per square inch (psi) and 140 degrees Fahrenheit). As a result of prudent economic analysis, significant savings were achieved by avoiding a single 6-inch pipe, which was available from a single supplier, and using dual 4-inch pipes. The savings were increased further by a three-week reduction in the construction schedule relative to the use of solid corrosion resistant alloy. However, due to the constraints of technology and manufacturer capabilities, RTP could not be adopted in water service projects where the parameter envelop is as high as 3,000 psi.
Applications Expansion
The forecast of 150-km length of RTP pipe in water injection applications for the Southern Area Oil Operations (SAOO) and Khurais areas laid the foundation for OMPPD to search the market for suppliers to provide 6-inch pipe that could withstand 3,000 psi. With the support of the Consulting Services Department (CSD), the Pipelines Project Department, and other organizations, a supplier was introduced to expand the applications that can leverage the cost savings of RTP using steel reinforcement technology. However, the sole source strategy did not support the economic business case of an RTP alternative as more suppliers were needed to reduce the cost through competitive bidding and to increase the bargaining power of the company.
Not long after, in 2017, the extensive research and capabilities verification efforts resulted in another supplier being qualified and added to RTP approved vendors. After a competitive bidding process, an order was successfully placed.
Continuous Cycle
Project Management and Engineering Services continues to work to increase RTP applications in OMPPD, but it requires continuous market intelligence of technological advances and being aware of vendors’ current capabilities — all in coordination with other organizations. By doing this, a new supplier has been identified that can produce an application to handle up to 2,250 psi at 221 degrees. CSD is currently working with the vendor to ensure completion of the required qualification tests and arrange a field trial in collaboration with SAOO. As the importance of project performance in terms of schedule and capital expenditure remain critical to Saudi Aramco business, facility life cycle costs are a paramount requirement for OMPPD. Progressively adopting RTP is a definite means to helping meet these scheduling and cost improvement goals.